Ist das Ideal, aus dem Material gebrauchter Batterien direkt wieder neue Zellen zu fertigen, erreichbar?
Der Markt der Elektromobilität wächst
Die Zahl der Elektroautos in Deutschland hat sich seit 2011 von 2.307 Elektrofahrzeugen auf 53.861 im Jahr 2018 gesteigert – bis 2020 sollen nach Plänen der Bundesregierung eine Million Elektroautos auf deutschen Straßen unterwegs sein.
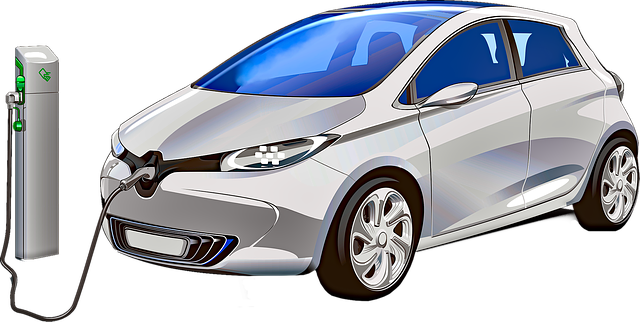
Ohne Rohstoffe keine Mobilitätswende
Um die hohe Energie beispielsweise beim Einsatz in Elektroautos bereitzustellen, enthalten Hochleistungsbatterien spezielle Materialien, die verschiedene kritische Rohstoffe enthalten. Dazu zählen vor allem die Stoffe Lithium, Kobalt, Nickel und Graphit. Die Nachfrage ist in den letzten Jahren enorm gestiegen: Über 40% des weltweit produzierten Kobalts wird für die Herstellung von Lithium-Ionen-Batterien verwendet (6). Kobalt wird aufgrund der geringen Reserven nur in wenigen Ländern der Welt abgebaut, darunter DR Kongo, Russland, Australien und Kuba. Die gesteigerte Nachfrage mit gleichzeitiger Abhängigkeit von Importen aus den Abbauländern hat zu einem massiven Preisanstieg geführt. Seit Mitte 2016 hat sich der Preis für eine Tonne Kobalt von 23.000 USD auf etwa 90.000 USD innerhalb von nur zwei Jahren fast vervierfacht. Die Industrie reagiert unter anderem damit, den Kobaltanteil weiter zu reduzieren, um Kosten zu sparen. Dies ist jedoch nicht unbegrenzt möglich.
Effizientes Recycling trägt zur Steigerung der Nachhaltigkeit der Elektromobilität bei
Das Ziel der Forschungsarbeit ist es, zu einer nachhaltigen Entwicklung im Sinne einer ökologisch intakten, ökonomisch erfolgreichen und sozial ausgewogenen Welt beizutragen. Das Recycling von Traktionsbatterien aus Elektrofahrzeugen wird in den nächsten Jahren massiv an Bedeutung gewinnen. Die derzeitigen Kapazitäten werden in absehbarer Zeit von der Menge an Rückläufern überholt. Generell sehen die Forscher der Fraunhofer-Projektgruppe IWKS am Markt ein hohes Potenzial für die Weiterentwicklung des Recyclings von Altbatterien von Elektroautos – im Idealfall bis hin zur vollständigen Kreislaufführung. Das Recycling von Batterien ist allerdings nicht neu und wird bereits im Industriemaßstab umgesetzt. Dazu gibt es verschiedene Verfahrensansätze:
- Mechanisches Recycling: Schreddern und Mahlen, Abtrennung von Fraktionen, Rückgewinnung von Konzentraten
- Pyrometallurgisches Recycling: Aufschmelzen der Batterien zur Rückgewinnung von Kobalt, Nickel und Kupfer
- Hydrometallurgisches Recycling: Auflösen von Fraktionen und chemische Rückgewinnung (Fällung, elektrochemische Abscheidung) der Elemente
Herausforderungen
Häufig werden die einzelnen Verfahren miteinander kombiniert, um so bessere Ergebnisse zu erzielen. Jedoch ist der Einsatz von Energie und Prozessmitteln je nach Verfahren noch recht hoch. Neben bereits etablierten Verfahren zur Rückgewinnung von Kupfer, Aluminium, Nickel, Kobalt und Mangan besteht noch Bedarf an effizienteren Prozessen, um auch anderer Bestandteile wie Graphit oder Lithium wieder zurückzugewinnen. Denn Lithiumbatterien sind wegen der darin enthaltenen wertvollen Metalle (Kobalt und Nickel) bereits heute schon rentable Abfallströme. Jedoch sollte im Sinne der werkstofflichen Kreislaufwirtschaft nicht nur die Rückgewinnung der Metalle, sondern die Wiederverwertung der höherwertigen Funktionsmaterialien (der Batterieelektroden) ermöglicht werden. Nur so kann die Elektromobilität zu einer wirklich nachhaltigen Alternative zu herkömmlichen Antriebstechnologien werden (neben der Bereitstellung klimaneutraler Elektrizität). Dazu muss die gesamte Recyclingkette von Batterien effizienter werden. Speziell steht das Recycling von Elektroautobatterien in Deutschland noch vor folgenden Herausforderungen:
- Altfahrzeuge werden (teilweise auf nicht legalem Weg) in andere Länder exportiert, anstatt sie einem Recycling in Europa zielgerichtet zuzuführen.
- Noch immer herrscht eine hohe Unsicherheit über die Rückläuferentwicklung. Dies hat zur Folge, dass Recyclingkapazitäten aufgrund fehlender Planungssicherheit mittelfristig nicht ausreichen werden, da die Unternehmen die Investitionen scheuen.
- Die Rückführlogistik ist noch nicht ausreichend aufgebaut, um von der Sammlung, über den Transport bis hin zur Verwertung sichere und effiziente Prozesse abzubilden.
- Hochleistungsbatterien gehören zu den Gefahrgütern. Dies bezieht sich nicht nur auf giftige Inhaltsstoffe wie beispielsweise Fluorverbindungen, sondern auch auf das bestehende Brandrisiko. Dies ist für jeden Schritt des Recyclingprozesses zu beachten und stellt hohe Anforderungen an Lagerung, Transport, Handling sowie das Recycling selbst.
- Bisher gibt es keine einheitlichen Batteriesysteme. Dies bedeutet, dass Batterien verschiedener Hersteller auch unterschiedlich aufgebaut sind. Das erschwert eine automatische Zerlegung und effizientes Recycling. Hinzu kommt, dass die Komponenten nur schwer voneinander zu trennen sind, z.B. durch Verklebung oder Verschweißen der Einzelzellen und der Gehäuse.
- Die bereits etablierten Prozesse wie die Pyrometallurgie bieten nur eine geringe stoffliche Recyclingquote bei hohem Energieeinsatz, daher geht ein großer Teil der Rohstoffe (vor allem die unedlen Metalle und der Kohlenstoff, also z.B. Lithium oder Graphit) verloren. Zusätzlich werden bei der Hydrometallurgie große Mengen an Prozessmitteln wie Chemikalien eingesetzt, die nach Abschluss des Prozesses wiederum einer fachgerechten Entsorgung zugeführt werden müssen.
Lösungsansätze
Es ist sicherlich noch ein weiter Weg, bis ein geschlossener Kreislauf in der Industrie etabliert ist. Nichtsdestotrotz gibt es bereits vielversprechende Ansätze, wie dies gelingen kann. Die Forscher der Fraunhofer-Projektgruppe IWKS empfehlen daher:
- immer den gesamten Wertstoffkreislauf der Batterien zu betrachten und nicht Verfahren unabhängig voneinander für einzelne Teilbereiche zu etablieren
- alle betroffenen Akteure, insbesondere Designer, Hersteller, Nutzer, Recycler und Kunden des Recyclingprodukts, einzubinden.
- Logistikströme mit fest definierten Prozessen zu entwickeln – von der Sammlung, über den Transport bis hin zur Lagerung.
- Sicherheitsrisiken bei Lagerung und Transport direkt in Recyclingkonzepte einzubeziehen und so zu minimieren.
- die Weiterentwicklung alternativer, innovativer Zerkleinerungs- und Trenntechnologien wie die elektrohydraulische Zerkleinerung, bei denen das Aktivmaterial Nickel-Mangan-Kobalt und der Graphit als Pulver leichter von den anderen Bestandteilen zu trennen sind. Ziel dabei sind die Reduzierung von Energie- und Prozessmittelverbrauch und die nahezu vollständige Rückgewinnung aller Bestandteile der Batterie.
- Möglichkeiten zur Automatisierung im Recyclingprozess voranzutreiben, u.a. durch verbesserte Kennzeichnung der verschiedenen Batterietypen und Verpflichtung der Hersteller durch Normierungen.
- eine konsequente Umsetzung eines Design for Recycling, d.h. Entwicklung und Umsetzung einheitlicher Konzepte, die die Wiederverwertung von Batterien und Akkus direkt bei der Entwicklung berücksichtigen (Voraussetzung für automatisierte Recyclingverfahren). Hierfür müssen alle Akteure miteinbezogen werden, also Hersteller, Zulieferer, Automobilbauer und Recycler.
- frühzeitig die Übertragung erfolgreicher Kreislaufkonzepte auf ähnliche Produkte prüfen, wie beispielsweise stationäre Energiespeicher.
- neue Ansätze bei Sammlungs- und Transportkonzepten zu gehen. Dazu muss u.a. die Rücknahmestruktur in Kooperation mit den Herstellern verbessert und ökonomische Anreize geschaffen werden. Die Konzepte müssen so gestaltet werden, dass ein Recycling nicht zusätzlich erschwert wird. Hierzu zählt zum Beispiel die Sicherstellung eines möglichst sortenreinen Stoffstroms.
Die Forscher der Projektgruppe IWKS konnten in einem Projekt zeigen, dass das Ideal, aus dem Material gebrauchter Batterien direkt wieder neue Zellen zu fertigen, erreichbar ist. Damit könnte der stoffliche Kreislauf der kritischsten Bestandteile von Lithiumbatterien geschlossen werden – vorausgesetzt, die notwendige Infrastruktur und Rahmenbedingungen werden entsprechend aufgebaut.
Kontakt: Jennifer Oborny, Fraunhofer-Institut | jennifer.oborny@isc.fraunhofer.de | www.iwks.fraunhofer.de
Technik | Mobilität & Transport, 17.01.2019

Der Zauber des Wandels
forum 04/2024 ist erschienen
- Windkraft
- Zirkuläre Produkte
- Tax the Rich
- Green Events
- Petra Kelly
Kaufen...
Abonnieren...
04
SEP
2024
SEP
2024
StiftungsApéro SommerTour mit Engagement Global
Wie machst Du das eigentlich in Deiner Stiftung?
CH-Basel
Wie machst Du das eigentlich in Deiner Stiftung?
CH-Basel
07
SEP
2024
SEP
2024
Halbtages-Fahrradexkursion „Raus-aus-fossilen Energien“
Veranstaltungsreihe "Mein Klima - auf der Straße, im Grünen und ... in meinem Stadtteil!"
80539 München
Veranstaltungsreihe "Mein Klima - auf der Straße, im Grünen und ... in meinem Stadtteil!"
80539 München
30
OKT
2024
OKT
2024
Professionelle Klimabilanz, einfach selbst gemacht
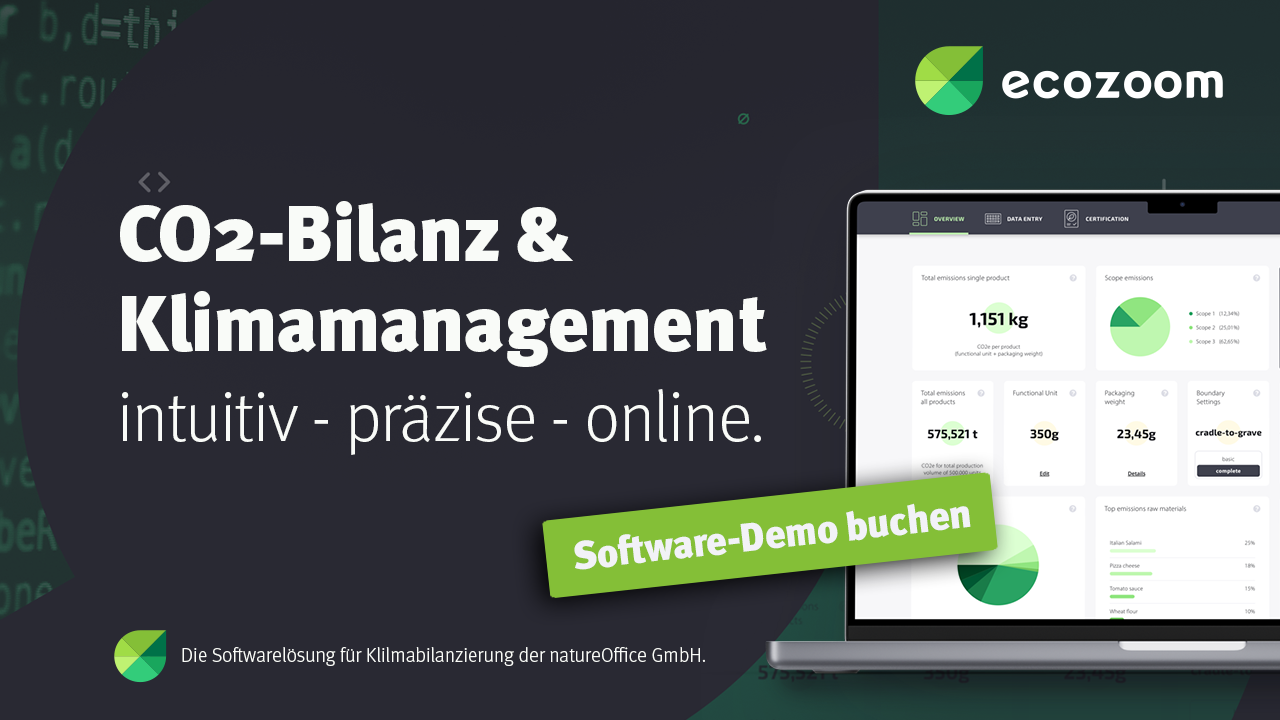
Einfache Klimabilanzierung und glaubhafte Nachhaltigkeitskommunikation gemäß GHG-Protocol
Politik
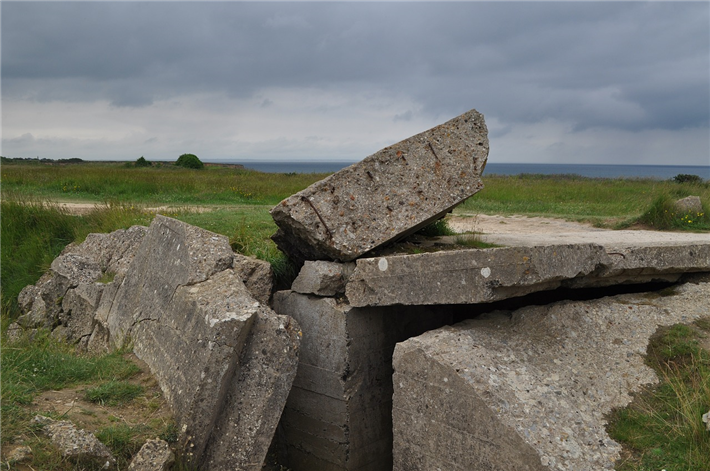
Christoph Quarch begrüßt die Feierlichkeiten zum D-Day in der Normandie.
Jetzt auf forum:
Achtsamkeit, Fürsorge, Krisenintervention
Die Arbeitsumgebung gesund gestalten
Ernährung als Gestaltungsbereich des Betrieblichen Gesundheitsmanagements
Betriebliches Gesundheitsmanagement und Klimaschutz:
Trends im Betrieblichen Gesundheitsmanagement